Routine Maintenance: Your Guide To Optimal Equipment Performance & Costs
Can the seemingly mundane act of routine maintenance truly revolutionize operational efficiency and financial stability? The answer, resoundingly, is yes. Routine maintenance, far from being a mere chore, is the bedrock upon which operational excellence is built, preventing costly breakdowns and optimizing resource allocation.
Their data from related equipment provides a foundation for constructing effective routine maintenance. If completed tasks are not reviewed regularly to gather feedback on instructions, tools needed, spare parts needed, and frequency; the maintenance process never gets better. Virtual technician® catches issues early, cutting downtime and repair costs by up to 20%. Fleet managers can use this data to schedule maintenance proactively. Train drivers for optimal operation, because driver habits impact maintenance costs significantly. Minimizing the impact of routine maintenance on operations can be achieved by scheduling maintenance out of peak hours. Predictive maintenance approaches and technologies can also be used to schedule maintenance based on the equipment's actual condition rather than a predetermined schedule, further reducing unnecessary downtime.
Routine maintenance is like the backbone of any operational system. Think of it as a preventative measure to avoid bigger, more costly problems down the line. Managing equipment failures and downtime. Maintaining equipment reliability is a major concern in any maintenance management strategy. Equipment failures and unplanned downtime are common maintenance management challenges that can disrupt operations and lead to significant financial losses. Routine maintenance keeps assets in good working order. Preventive maintenance refers to regular, planned maintenance of equipment and facilities to prevent unexpected failures or breakdowns. Unlike reactive maintenance, which addresses problems after they occur, preventive maintenance aims to keep machinery, equipment, and systems running smoothly by addressing potential issues before they develop into significant problems.
- Les Kassos The Hilarious Animated Series Its Quirky Characters
- Michael Ches Wife Leslie Unveiling Their Relationship Secrets
The article is more of a concept, so providing a bio data table is not relevant. So, I will provide a table containing information related to the subject.
Category | Details |
---|---|
Definition of Routine Maintenance | Planned, ongoing maintenance to identify and address problems before equipment failure. |
Key Goals | Optimal working condition, preventing unexpected failures, prolonging equipment lifespan. |
Benefit for the Business | Less expensive and disruptive than emergency repairs, minimize downtime, optimize resource allocation, and better control operational costs. |
Typical Routine Maintenance Issues | Shortfall in structure and scheduling, poorly defined task lists. |
Importance of Review | Regular review of completed tasks to gather feedback on instructions, tools, spare parts, and frequency to improve the process. |
Proactive Maintenance | Scheduling maintenance out of peak hours to minimize operational impact. |
Predictive Maintenance | Utilizing technologies to schedule maintenance based on equipment condition, reducing unnecessary downtime. |
Impact of Driver Habits | Training drivers for optimal operation as their habits significantly impact maintenance costs. |
Preventive vs. Reactive Maintenance | Preventive maintenance aims to prevent failures, while reactive maintenance addresses problems after they occur. |
Comprehensive Approach | Addressing problems arising from personnel, maintenance practices, hardware, and systems. |
Role of AI | Ai addresses this by continuously monitoring the condition of assets and adjusting maintenance plans in real time. |
Fleet Management Services | Consider hiring fleet management services like universal fleet solutions (ufs). |
There are many ways to overcome the biggest maintenance challenges in manufacturing. With technology evolving and several maintenance processes like predictive maintenance becoming much better over time. The maintenance management, routine tasks are only part of the equation. From a business perspective, routine maintenance is valuable because its typically less expensive and disruptive than emergency repairs. Implementing routine maintenance as an organization can, in most cases, minimize downtime, optimize resource allocation, and better control operational costs.
It presents feasible solutions to typical maintenance challenges that may occur in any department, ranging from staffing to routine maintenance to resolving intricate issues, equipping organizations with the necessary resources to streamline their operations, boost productivity, and attain their objectives. Your prevention efforts must be comprehensive and cover all areas from which problems may arise, such as personnel, maintenance practices, hardware and systems. These categories are most useful when solving cause/effect problems. However, they may also be used to keep a manager focused on all aspects of maintenance. Your maintenance team may have difficulty understanding what kind of attention to pay to what equipment, when, and how. In addition to your maintenance manager, consider hiring fleet management services like universal fleet solutions (ufs). They can help determine your average spend on equipment
- Download Bollywood Hollywood Movies Latest Releases More
- Movierulz Latest Telugu Kannada South Film Updates Alternatives
Thats why in this comprehensive guide, we are going to describe what is routine maintenance and the difference between routine maintenance and preventive maintenance. Routine maintenance is any planned, ongoing maintenance that is undertaken to identify and address problems before they can lead to equipment failure. Routine maintenance falls into several key categories, with each aiming to keep equipment in optimal working condition, prevent unexpected failures, and prolong equipment lifespan. By understanding the different types of routine maintenance, organizations can tailor their maintenance strategies to address specific needs, ensuring equipment runs, It presents feasible solutions to typical maintenance challenges that may occur in any department, ranging from staffing to routine maintenance to resolving intricate issues, equipping organizations with the necessary resources to streamline their operations, boost productivity, and attain their objectives. Your prevention efforts must be comprehensive and cover all areas from which problems may arise, such as personnel, maintenance practices, hardware and systems. These categories are most useful when solving cause/effect problems. However, they may also be used to keep a manager focused on all aspects of maintenance. Your maintenance team may have difficulty understanding what kind of attention to pay to what equipment, when, and how. In addition to your maintenance manager, consider hiring fleet management services like universal fleet solutions (ufs). They can help determine your average spend on equipment
Managing equipment failures and downtime. Maintaining equipment reliability is a major concern in any maintenance management strategy. Equipment failures and unplanned downtime are common maintenance management challenges that can disrupt operations and lead to significant financial losses.
A powerful cyclonic storm, showcasing the immense force of nature and the need for preparedness. In 2020, cyclone amphan swept through the bay of bengal, leaving a trail of devastation in its wake. This keeps it running smoothly, helps it last longer, and avoids costly surprises when something breaks down unexpectedly. Routine maintenance keeps assets in good working order. A list of tasks, each beginning with check and no other guidance has very little
The global commercial real estate market is anticipated to reach an impressive value of $118.80 trillion by 2024. This immense growth highlights the critical importance of maintaining commercial buildings. Find solutions to building maintenance challenges like preventive maintenance, asset tracking, cost management, and improving tenant satisfaction.
Ai addresses this by continuously monitoring the condition of assets and adjusting maintenance plans in real time. When an anomaly is detectedsuch as unusual vibration in an hvac systemai can instantly trigger an emergency repair task while simultaneously adjusting the routine maintenance schedule to accommodate this unexpected event.
From a business perspective, routine maintenance is valuable because its typically less expensive and disruptive than emergency repairs. Implementing routine maintenance as an organization can, in most cases, minimize downtime, optimize resource allocation, and better control operational costs. Your prevention efforts must be comprehensive and cover all areas from which problems may arise, such as personnel, maintenance practices, hardware, and systems. Your maintenance team may have difficulty understanding what kind of attention to pay to what equipment, when, and how.
- Hamza Taille Biographie Plus Tout Savoir Sur Le Rappeur Belge
- Explore Masa49 Events Pilates More Latest Updates
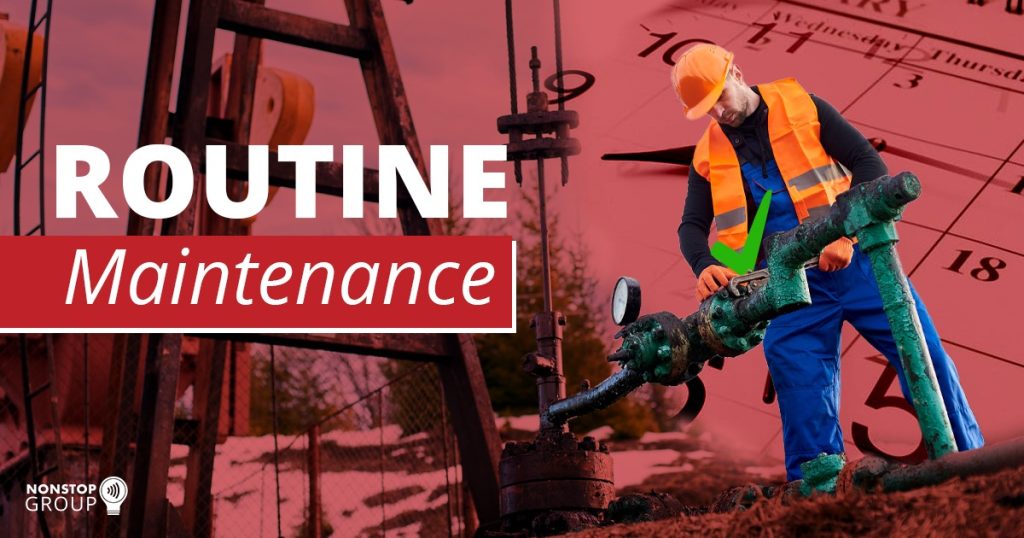
Routine Maintenance A Beginners Guide To Routine Maintenance Workflow
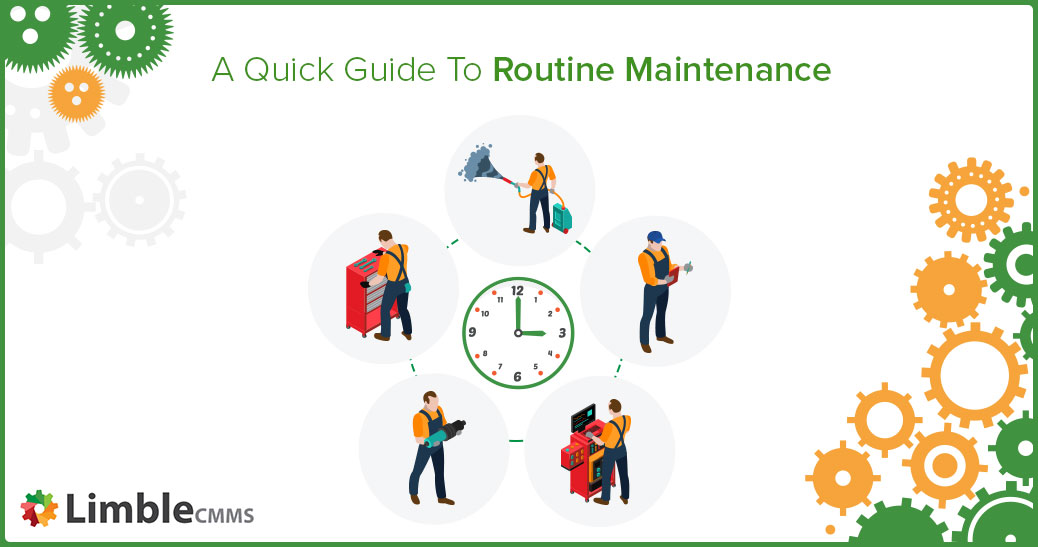
A Complete Visual Guide To Routine Maintenance Limble CMMS
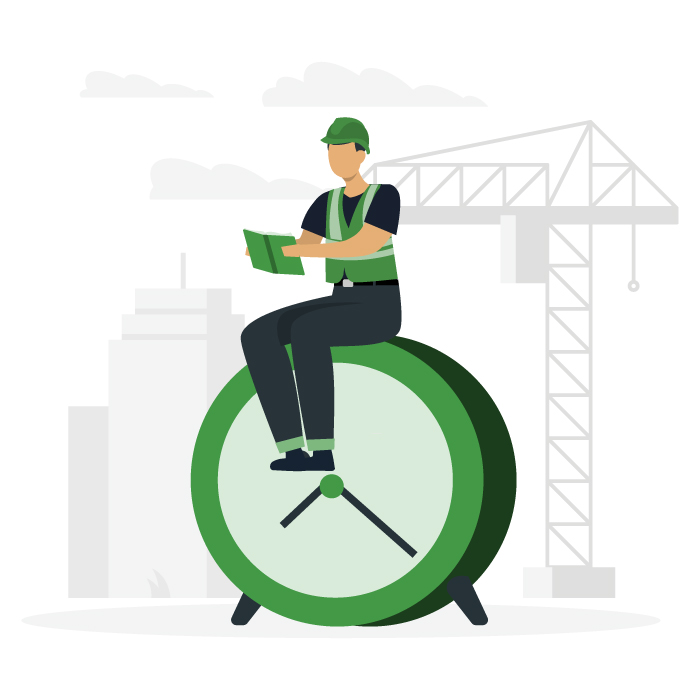
A Complete Visual Guide To Routine Maintenance Limble CMMS